Bench
Top Power Supply -- Part 1,2,3.
© Tony van Roon, VA3AVR
"This 30 volt Bench Top Power Supply is rated at 10 amp, and it
is so versatile and powerful that it will slowly turn your regular 115VAC power drill. It was designed to work under
the most extreme circumstances and short-circuit protected (within specs), even in the 10-Amp setting. Cooling
(optional) fan(s) keep the semiconductors and the large cooling rib cool automatically."
Introduction:
This "jumbo" power supply is built around the monolithic volt regulator IC from Motorola, the MC1723, which is a more
modern version of the old uA723 from Fairchild Semiconductors. Other versions of this IC, like the LM723 from
National and others, and even the old MC723 metal-can will work too. Though the prototype of this powersupply used the
ceramic military version of the 723. The uA723 voltage regulator was designed by Bob Widlar and first introduced in 1967, and used
ever since. It is a flexible, easy-to-use regulator with excellent performance. Looking at Fig. 1.,
this 14 pin regulator is not of your average type. You find this regulator everywhere, in a variety of applications
including military. This IC can function both as a positive or negative voltage regulator and designed
to deliver a load-current of 150mA DC. With external 'pass' transistors the output current can be increased to
significant levels, as in our project to about 10 amps (depending on your transformer). A special temperature
monitoring circuit (optional) will activate two to four CPU fans (optional) automatically if the temperature of the
large cool rib exceeds an adjustable temperature and activate or deactivate the fans within a 2.3°C temperature
variation. Pretty good for a 'cool' rib in my opinion. Even at 1 amp the cool rib may get warm, but at 10-amp
it gets really hot and so the fans will not only keep the temperature at a safe level it also is an added safety
feature to give this powersupply a life-span of at least 30 years! The semiconductors in the shaded, light yellow
area on the Circuits Diagram below go all on the large cool rib. See Fig. 5.
Voltage Output in 'Low' setting is variable from 0.7 - 6 volts (more later why the 0.7V), in the 'High' setting the
voltage is variable from 3 - 30 volts. Current is adjustable in the 'Low' position from 0 - 1 amp and in the 'High'
setting from 1 to 10 amps. 0.1% line and 0.03% load regulation. Ripple is less than 0.001Vpp. Scale tolerance Low:
0.2%, High: 0.5%. Another welcome feature is the short-circuit protection. Beautiful chip. The normal commercial
temperature range is 0°C to 70°C (MC1723CD, CL, CG, and CP package). The military version (MC1723G or L) can
handle a temperature range of -55°C to +125°C. That one you can really freeze or cook!
Voltage Regulation:
Shown in Fig. 2. was the initial idea of voltage regulation and method we will be using. As
mentioned before there are two scales, 0.7 to 6 volts and 3 to 30 volts. A nice problem way to do that is with a
DPDT switch (S2). Plus we will add a Led to indicate which scale we are on. This toggle-switch switches both the
volt-scale and the volt-meter. In Fig. 3. you can see how, by putting one side of S2 to
ground via one resistor, the output voltage is in the 3 - 30V scale, and the other side of S2 via another resistor
(R-extra) to switch to the 0.7 - 6 V scale. At the same time we switch a parallel resistor with it as a shunt for the
panel-meter. If we calculate the value of this resistor to represent the meter Ri for the 6V scale, then
everything is a piece-of-cake. A single pole switch is in this scenario sufficient, without limiting any performance.
A second pole is used to switch the led-indicators, making S2 a double-pole-double-throw type. The 'Voltage' on the
front panel is controlled with potentiometer R3 and the scale adjusted with trimmer pot R2.
The Led indicators have a voltage of between 1.8 and 2.0 volts dc
and the current no more then 25mA max. They can also use be used to glow on AC, only then an extra diode will be
required (see Fig. 4.) which also protects the Led's just in case we accidentally connect them the wrong way. Point
'A' is connected to the same as indicated on the circuit diagram. Leds D6 & D8 are for the 30-volt and 10-amp
respectively and D5 & D6 are the 6-volt and 1-amp settings but are not lit because they are shorted by the switch
S2b and S3b. Resistors R28 to R31 are chosen accordingly to input voltage. A rule of thumb is about 100 ohms per
volt input voltage. This means a little less than 10 milliamps per Led and that is enough to light them up. Depending
on the Led type you use (regular, high-, or ultra brightness) you may have to adjust these resistors to suit your needs.
You could use trimmer pots instead of resistors but that is such an overkill and waste. So, not needed, just a bit
of tinkering may be required. The method of short circuiting the unused leds was chosen since this was the simplest
and cheapest way of going about it. They also serve as a "On/Off" indicator of the power supply when it is switched
on because a minimum of two led's will always be on. It is okay to use two bi-color leds but they are more expensive.
Part 2 - of this project will start with the construction of the large cool rib,
mounting and wiring up all semiconductors, and (optionally) the cooling fans. Then the back panel and the 115VAC
wiring of the on/off switch, transformer, fuse holder and powercord/receptacle, and last the bridge rectifier BR1
and the large electrolytic capacitor C3. There are lots of photographs and pictures to help you get through all
this. The Printed Circuit Board and Lay-out are also available in Part 2. The finished product is a worth while
project and outperforms many commercial units.
"In this second part of the Bench Top Power Supply
project we will cover the construction, assembly, and wiring of the large coolrib and the optional Automatic Fan
Control circuit. When that is done the transformer T1, 115VAC components, large capacitor C3, and the bridge
rectifier will be installed and wired up. There are lots of pictures and photos to help you out. Main thing to
remember is to TAKE-IT-EASY, read the explanations and take your time. This is definitely a NO rush job."
The Large Coolrib:
Building the large coolrib was a lot of fun. I found an old coolrib in one of my parts boxes which measured about
11" x 4-1/8" (28 x 10.5cm) which is perfect because it fitted the back of the Hammond Instrument Case perfectly with
room to spare for the AC-side (see photo). The Hammond Instrument Case is not cheap, but is a ventilated, low-profile,
series 1426V type with dimensions of about 12x8x4 inches. Make sure
YOUR transformer fits your instrument case!
Looking at the photo above, it shows the large coolrib with the two cpu fans. Since that picture was taken I
have upgraded to three ball-bearing cpu fans which have more blades and run quieter. They also are of a different
model and required a bit of tinkering to mount them on the coolrib without drilling more holes. But that's the fun part
of it, making things fit and work. I didn't say building this power supply was easy, well, what I mean by that is that
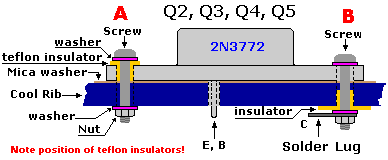
some stuff needs to be modified in order to use it. I mounted the fans in such a way so they blow the cool air over the
semiconductors and the coolrib instead of sucking the hot air away from it.
Try to do a good job on the coolrib, it'll pay later down the road. I mention this because we are not all Tool-and-Die
mechanics and for some of us this can be a real chore. But don't worry, just take your time and you get it done. It
took me almost a week on and off. A lot of wires need to be hooked up and so that takes time.
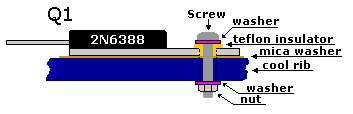
Before starting to mount the transistors and power diode D3, make sure all the holes are drilled. Take a large drill bit
and remove the burrs. (Tony's note: D3 has been upgraded to a TO-200 model @ 20A in early 2009)
Including several extra holes to feed the wires through from D3, the transistors and a spare just
in case. Once everything is wired and bolted together it is pretty hard to drill any hole anywhere. I'm not inclined
to give drill bit #'s and hole sizes at this time. Just make sure the holes are large enough to snug-fit the plastic
hole-insulators.
Mount the TO-3 power 2N3772 (or NTE181) transistors, Q2, Q3, Q4, and Q5. Use silicon heatsink
compound on all semiconductors mounted on the coolrib, between coolrib, mica-washer, and transistor. Use insulators
to screw down the transistors. Use the photo's and drawings as a guide if you are not familiar with this method.
That done, mount the TO-220 transistor Q1 (2N6388 in my case). Again, make sure it is mounted insulated.
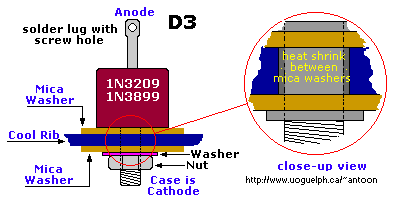
Power diode D3, needs some pre-work if you use the stud-mounted
model, like I did. The
two mica washers and heat-shrink tubing makes sure that this component also is
insulated from the coolrib (see pictures). Note again that D3 uses mica washers on each side of the coolrib and a
bit of heat shrink tubing in between, the size of the thickness of the coolrib, to prevent the stud from touching the
coolrib via the inside of the mounting hole. You need to drill the hole a little bigger to account for the extra
thickness of the heat shrink tubing. Shrink the heat-shrink with a hairdryer or something to make it a sturdy fit.
Try to make it a good fit as possible inside the mounting hole but not tight. Meaning, after you drill the two holes
for D3, one for the stud-mount, the other to feed the wire through, check if the diode with the heat shrink fits the
hole. If not, don't use force and drill it a little larger or use a small round file. Remove all the burrs from the
holes with a large oversized drill to prevent shorts. The nut of D3 faces towards the back.
DO NOT OVERTIGHTEN D3 (studmount version)!
I left the photo's pretty large so you can have a better look. For good heat transfer from the semiconductors to the
coolrib, use silicon heat-sink compound/paste of some sort. They come in clear and white colors. Use it also on the power
diode d3.
When all semiconductors are mounted, and
BEFORE starting to wire the whole thing up to the circuit board,
take your continuity tester or multimeter and verify that the body of all transistors (Q1 t Q5) and the stud of D3 are
insulated from the coolrib and each other, meaning
NO continuity on all of them. One probe on the coolrib and
with the other you check the case of all (collector) of all semiconductors. If all is well, proceed, if not and you
notice continuity somewhere it means that that part is not insulated properly.
Fix that first before continuing!
Click on the
D3 photo's for a full-size view.
Making a good and solid
Printed
Circuit
Board will have its own awards. The trimmer pots for
'voltage' and 'current' adjustments are logically grouped together for neatness and ease of use. Use thick wire to
connect the collectors of Q2 to Q5 to the positive of C3. By full scale in the 10 amp setting there is 10 amps going
through. Thick wire is mandatory or it will burn. Do the same for the wire going from the minus of C3 to the
common ground connection on the pcb (see lay-out). From this point to the output jack-posts, thick wire also. Make sure
large capacitor C3 is mounted isolated from the case or else, because of large currents, weird things may happen
inside the case. C5 and C6 must be of the tantalum variety, nothing else!
When you mount the pcb in the case, remove the copper around these screws so the pcb will be isolated from the case.
This method will prevent unwanted spurious ground loops.
Please note: New PCB & Lay-out
below. Makes wiring up the PS3010 easy! Unfortunately not included in the KIT version yet.
Wire-wound resistors R10 and R11 need to be mounted 'raised' from the pcb because they may get hot and placing them
on ceramic standoffs or something will prevent burning the pcb in that area.
Diode D3 and transistor Q1 are drawn on the layout but are actually mounted on the large coolrib, so take note.
When you are ready to wire up the switches then it is important to know that they are drawn in the 30-volts (S2a) and
10-amps (S3a) positions.
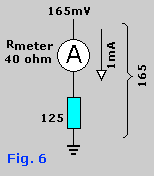
The Panel Meters:
A big boy like this Jumbo power supply earned to have a set of good panel meters. In the prototype a set of 1-milliamp
full-scale units were used. But I leave it to your own fantasy and creativity how to solve the problem to enhance the
overall cosmetic view of this power supply. As you can see on circuit diagram (Fig. 5, Part 1), both meters have four
switching resistors. Two of them are mounted permanent in series with the measuring system, the other two are
paralleled by means of a switchable section.
You should get panel meters with a very low own current use and on top of that if possible types with 30 or better
still 60 indicator stripes (or markings) on it. A low current usage also means a low internal resistance (R
i)
which will benefit in the area of current measurement of that particular panel meter. We assume that in the low 0 to
1-amp setting there are only small voltages available over R10-R11 and if all goes to plan is the maximum voltage
around 165 millivolt and that is for low-ohm meters feasible. So, try for a model with about 100 millivolt at
full-scale. Which means that a 100 millivolt type only pulls 1 milli-amp at full scale. A 100µA type will
have a R
i of about a 1000 ohm. Check it yourself with Ohm's Law. For the current panel meter try to get a
type with 50 or 100 indicator stripes (or markings).
This is less critical for the 'Volt' unit. Basically you can use any model as long as its own power is not higher
than a couple milli-amps. The internal resistance or R
i is less important since any type of internal resistor
will be removed anyways. Both 7-Segment and digital meters will be added later this year.
To calculate these resistors (R17 to R20 for
current, R24 to R27 for
voltage), you have to determine your
meter's specifications. And here again, play with Ohm's Law. Point is that in both cases, for current and voltage,
we measure
voltage every time. For the measurement of current is
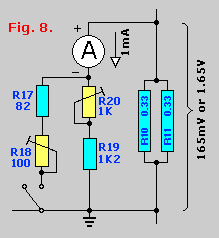
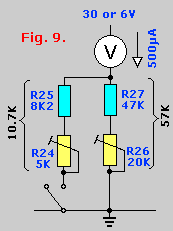
that 165 millivolt in the 1-amp position and 1.65 volt in the 10 amp position. An example is given to make that
very clear. Imaging we have a unit which at full deflection pulls 1 milli ampere and has an internal resistance of 40
ohms. If we want this unit to measure 165 millivolts then we have to calculate the values as shown in the
Fig. 6. example. The 165 mV is the voltage, so the current has to be 1 milli-Ampere, using ohm's law
that gives us a total resistance of 165 ohms. This is the total resistance of everything. To get the value of the
shunt resistor just deduct the internal resistance. So, the shunt resistor has to be exactly: 165 - 40 = 125 ohms.
To comfortably be able to adjust the meter's deflection we divide this up in regular resistor of 68 ohm and a trimmer
pot of 100 ohms. The desired value of 125 ohms lays somewhere in between. But we are not done with that. We still have
to take the 1 - 10 Amp setting in consideration because there are already a couple shunt resistors in series with the
meter and those are the components for the 10 amp scale. Looking at the
example in
Fig. 7,
we have to measure there 1.65 volt and that means a resistance value of 1650 minus 40 is 1610 ohms. This weird
resistance value can be obtained with a regular 1.2K resistor and a trimmer potentiometer of 1K.
The required value of 125 ohm can be acquired by adding another resistor parallel with the funny 1610 ohm one.
Doing the math (ohm's law), it turns out the value of this parallel
resistor is about 135.5 ohms and that is easily obtainable with a 68 ohm resistor plus a 100 ohm Bourns trimmer
potentiometer. And if you're a perfectionist you can even choose a 82 ohm and a 100 ohm trimmer potentiometer. In the
end you will be getting something as shown in
Fig. 8. If you have different types or values
of panel meters, the math is exactly the same. The trimmer pots with do the rest.
The indication for the Volt-meter is similar. Note that we have taken a 500uA meter as an
example! I mention again, you have to find out the characteristics for the meter
YOU are using. (No, I will not do
the math or other calculations, please do it yourself I don't have the time). It is not all that difficult. Simply
assume we're measuring in the 6 and 30 volt ranges which happens to occur with a lot easier resistor values. Let's
say we have a panel meter with an 'internal resistance' of 3000 ohms and that at full-scale it uses about 500uA,
then the shunt resistors are looking like this: for 30 volt the circuit needs a total resistance of 60K, so we need a
57K as shunt which is put together of a regular 47K resistor plus a 20K trimmer potentiometer. For the 6 volt scale
we need a total shunt of about 9K which is put together by putting a 10.7K resistor parallel with a 57K resistor.
Again a strange value but 8.2K plus a 5K trimmer potentiometer will make it work. In
Fig. 9 I used, where ever I could, metalfilm resistors instead of the regular carbon type. They are more temperature stable.
But carbon types will work fine.
Shown above is the circuit diagram for the automatic temperature control switcher. The thermistor, a 1.7K at
70°F model available from Radio Shack (not sure), will keep tab on the coolrib's temperature (adjustable with a
10-turn trimmer potentiometer P1) and activate the cpu fans (or one larger fan) to keep things cool. This circuit is
not part of the Power Supply PCB at this time, but (given time) I will change that early in the new year. I played with several
different value thermistors; 1.7K, 5K, 10K. They all worked fine after playing with the resistor network a bit.
The D1 diode can be a signal diode like the 1N914 or 1N4148 for micro relays, use a 1N4001 or higher for relays above
100mA. D1 acts like a spark arrestor/filter when the coil is de-energized.
"Almost done! In this part three we install the final
parts, make the last connections, and do the final adjustments with the trimmer pots.
Take your time (go-slow) with the trimmer pots for adjusting current! "
Where applicable, click on the picture for enlargements. Above you see the photo of my finished model. Looks good,
performance is excellent, and I am very happy with it. Notice however that the panel meters are shown non-modified,
meaning that I added and modified the stripes for the two settings after the picture was taken. I don't own a digital
camera so am dependent on others to help me out.
I purchased a brand new transformer, model 165S30 manufactured by Hammond. It is of the regular kind. You can get a
'low-profile', horizontal type which mounts a bit lower. Whatever model you have or buy make sure it fits your case
including the large capacitor. The 30V type is only required if you need the full 10A, otherwise a 22V-28V type will
do fine. A CT (Center Tap) is NOT used.
The 165S30 transformer has 5 wires, the primary side has two black wires which are connected to your 115 vac. The
secondary has 3 wires, in my case two green and one green/yellow. The green/yellow is not used. Isolated it with
some heat shrink and tie it up, see Fig. 10. I never cut the wire off. The two green wires go to your Bridge Rectifier.
It is probably marked 'AC' or '~'. Make sure the transformer makes good ground with the chassis, which in my case
meant removing the paint. I then use a file to take the varnish off one bottom corner of the transformer. When you
finish mounting the transformer into the case, take a multimeter or continuity tester and make sure the chassis of the
transformer makes good connection with the chassis of the power supply.
The fuse is a 3.15A slow-blow type to prevent it blows when you switch on the power supply with a bit of load. This
transformer is a real heavy one and weighs several pounds. If you're planning to use it with heavy loads, I would
suggest to get one which can provide 12-15Amps at a desired voltage, but, the 10-amp transformer listed in the parts
list will work. The difference is that the 10 amp transformer gets pretty hot if you use it at the maximum current. If
you would have a 12-15 amp type it will only get a little warm. In my case, I do use the 10amp setting often but
not for extended periods. Several minutes at best. Usually around 7 amps or so for charging purposes.
It is probably best to mount the Bridge Rectifier, fuse holder, and power cord first before bolting down the
transformer. As you can see in Fig. 11, I used a mounting bracket for the large capacitor, this bracket is also
mounted on the back panel so don't forget to drill the holes first. I used a 115vac receptacle, fuse, and on/off
switch combination which I salvaged from an old UPS and the whole thing is mounted on the back panel.
Crimp spades onto the two secondary green wires and mount the transformer. Connect those wires to the Bridge Rectifier
as mentioned earlier. Install the large capacitor and wire up to the '+' and '-' of the Bridge Rectifier. From this
point on all other '+' and '-' connections are taken from the large capacitor terminals. Use thick wire.
As mentioned earlier, instead of a Bridge Rectifier you could use four separate 'stud-mount' diodes and make your own
bridge. The two anti-rattle capacitors, C1 and C2, should be mounted directly onto the transformer or the bridge
rectifier for best performance. Power diode D3 is a very vital component in this power supply and so was chosen a bit
over-rated to make sure it will perform satisfactory under all circumstances and temperature changes. You probably
already know that a diode is temperature sensitive which is most noticeable in the 0.7Volt range. Since the same D3
also has a job of current limiting it is best to make sure this diode does not get too hot. So, we really want a
solid diode of 20 amps minimum.
In case of a short circuit, there is at least 2.5 amps of current going through each power transistor, and that is a
lot at about 60 to 70 watts of dissipating energy. That is why the 2N3772 power transistors come in which can
dissipate 350 watts or so. And so, as a matter of speaking, at 30 volts we could well assured short out the output
jacks and fry an egg on the output power transistors.
Now lets have a look at L1 & L2. L1, C9, L2, and C10 are soldered as close as possible to the output jacks. We even
have to cut the solder leads as short as possible. C10 is soldered directly on to the '+' and '-' output jacks. C9 is
soldered parallel over the L1/C10/L2 network. The two thick wires coming from the printed circuit board are soldered
onto each leg of C9. Oh yeah, I mention again that the PCB has to be mounted
isolated from the case. The common ground connection is connected to the '-' jack via L2. This is a little bit of tinkering
but can be done easily. We are working here with 10 amps so worth all the efforts. The new PCB will have screw connections
to make the connections easy.
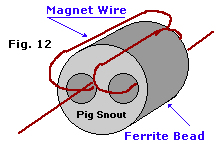
I call the ferrite beads "pig snouts" because that's
what it looks like to me, but hey, call it whatever you want. You need to make two of them. On the circuit diagram
they are indicated as L1 and L2. One or two turns of thick magnet wire will do the trick. L1 and L2 will keep the
output jacks clear of high-frequency interference. Can you omit them? Certainly if you don't care about that feature.
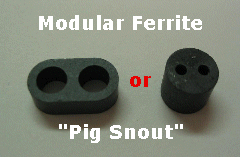
By now you must be anxious to try everything out. Well, be patient, we're almost done. We still have to adjust the
eight trim potentiometers on the pcb. And you really
need to sit down for it and carefully take your time. Look for a
time and place when you can do this quietly and undisturbed. The last thing you want is to open this heavy power
supply up again and re-adjust it because of initial sloppy adjustments. So, take your time, go slow, and verify each
adjustment until you're satisfied.
The adjustments are done in a special sequence and if you keep yourself to this procedure then I doubt you would
encounter any problems. Okay then, here goes it.
Adjustment procedures:
FIRST check for correct wiring from and to pcb, jacks, meters, and coolrib. Very important.
Before starting the adjustments, familiarize yourself with the trim pots on the printed
circuit board and the potentiometers on the front panel. The two on the front panel are R3 and R12, the others are on
the pcb. I mention this to avoid confusion while doing the adjustments. If you wish, mark all the pots ahead of time
by writing the 'R' numbers on a piece of scotch tape or something. It will help a lot!
Important: make sure to 'zero' the panel meters with the little plastic screw attached to the needle movement
unit.
Open up the connection of the thick wire between the pcb and the positive of C3 and insert a small fuse of a couple
hundred milliAmps. If you don't have a small fuse handy then you can also use a 1/2 watt 10-ohm resistor or something
similar. Do NOT plug in the power supply yet! Turn all trim pots to the left (counter-clock-wise) all the way. Set the
two potentiometers on the front panel about halfway. Set the two switches on the front panel (1/10A, 6/30V) to the low
settings, meaning the current switch on 1 amp, and the volt switch on 6 volt.
Take your digital multimeter and secure its minus (black) lead on the minus output jack. Plug in the power supply and
switch on the power. If all is well and there is no smoke, the main fuse and small temporary fuse on C3 remain okay, we
can continue.
Put the plus (red) multimeter probe on topside of potentiometer R3. This is the position closest to the minus of C4 on
the pcb. You have to measure there a voltage of precisely 6 volts.
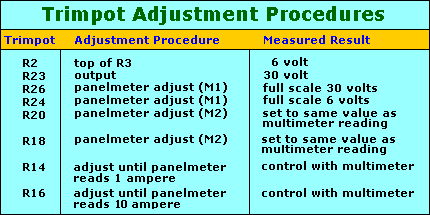
If needed, this voltage can be adjusted by turning the R2 pot. Turning the potentiometer (R3) on the front panel will
move the panelmeter but NOT the multimeter. If you move the red probe to the '+' output jack and you should find a
variable voltage (via R3) between 0.7 and 6 Volt.
Don't worry about the current meter at this time, it probably will not move at all because there is no current. All
you do at this time is adjusting the low-voltage scale.
Leave the multimeter probes connected to the '+' and '-' output jacks and switch the Volt-switch (S2a) on the
front panel to the 30 Volt position. You will see that the voltage makes a big jump upwards. We adjust R3 all the way
to the right (clockwise) and adjust trimmer potentiometer R23 until your
multimeter shows 30 volts. We now
adjust R26 until the panel meter shows the same, 30 volts. Switch back to the 6-volt position and adjust the panel
meter to 6-volt full-scale with R24. If you're done with this and you are satisfied then have beer on me for a job
well done. You are half way finished!
Switch off the power,
unplug the powercord. Remove the temporary fuse between the
positive of C3 and the pcb and re-connect the wire to start adjustments on the current settings.
Switch the panel meters to the 6 volt and 1 amp positions and turn current-limiter R12 on the front panel all the
way to the left (counter-clock-wise). Set the volt meter on the frontpanel to 4 volt with R3. Select a setting on your
multimeter of 100 or 300 milli-amps dc. Take the red probe and insert a resistor of 39 ohm between the red probe
and the '+' of the output jack. You will notice that current flows through that resistor. The panel meter also shows
a bit of current and at the same time the needle of the panel-voltmeter falls back a little to about 2 volts or even lower.
If that is the case you know your current limiter is working properly and you can continue with the adjustment
procedures.
Remove the 39 ohm resistor. Switch your multimeter to the highest current setting (preferably 10A) and connect it
directly to the '+' and '-' output jacks. The meter should show no more current than with the 39-ohm resistor, even
less this time. Carefully open up R12 (front panel) clockwise until you see increased current on both multimeter and
panel meter. A good multimeter will go to at least 10 amps, but I guess the job can be done with 2 or 3 amps also.
On the other hand It would be actually better to borrow a good multimeter from a friend or rental shop if you don't have
one yourself.
Okay, on with it. Open R12, slowly, as far as possible and note the current reading.
REMEMBER you are still
at the 1A/6V setting! If there are no problems the current reading probably shows 1/2 amp or something in that
area. Let it sit in that condition for awhile and observe the temperature of the large cool rib. It should warm up a
little bit. If all is okay and still no smoke you can safely assume that the circuitry works correctly.
Before continuing:
Please be aware that 10 amp is a lot of current. Any carelessness on your part will cause damage, guaranteed! I can't
stress enough to do these adjustments without disruption and with great care. Over-adjusting any of the current-trimpots or
adjusting them too fast will surely blow one or more 2N3772 power transistors, or 2N6388, and possibly other related circuitry.
Okay, on with it--carefully.
The following adjustments have to be done in the correct sequence. Switch the power supply
OFF. Set the panel switch to the 10-Amp setting and also the multimeter to as high a current setting as possible. Turn
R12 all the way to the left (0 amp), the multimeter is still connected to the '+' and '-' output jacks on the front panel.
Turn the power supply
ON. You should notice almost no current at all. The setting of the 'Volt' potentiometer (R3)
does not matter much at this time so don't worry about it. Carefully and slow adjust R12 to a high as possible value and stop
when it shows about 5 amps on the multimeter. Adjust the panel meter with R20 until it shows the same value as the
multimeter. When you're done the panel meter should show half way the 10-A scale. Just make sure that your
multimeter can handle 10 amps. If not, then don't exceed that value with R12 or you blow up your multimeter. Adjusting the
PS3010 at 5 or 8A is acceptable too.
Turn R12 again all the way to the left and flick the switch on the front panel to the 1-A setting. Adjust R12 all the way
to the right and with R18 adjust the value of the multimeter with the value of the panel meter until they're equal.
In the mean time the coolrib is getting quite hot during all the adjustments in the 10-A settings. But that is done
now. You have now adjusted six of the eight trimmer pots and so still two to go.
Remove the multimeter. Turn both potentiometers on the frontpanel (R3/R12) all the way to the left (0 position).
Return the switches to the 1-A and 6-V settings. Short out the output jacks on the frontpanel with a piece of wire.
Turn R12 all the way to the right and adjust R14 until the 'current' panel meter indicates precisely 1-amp (full scale).
That done, turn R12 back all the way to the left and place the current switch in the 10-A setting. Adjust the
full scale of the panel meter with R16 until it shows exactly 10 amps. At this setting the cool rib heats up quickly so
keep an eye on the temperature. You are done. Finished. I'll bet you are smiling now. After all, you now have an
analog piece of equipment equal or better then the commercial unit and for a fraction of the cost.
AGAIN: Be careful when adjusting the 10A settings! Adjustments with the trim pots
to adjust the current should be done very SLOW or you're guaranteed to blow one of the 2N3772 power transistors and/or
other related components.
*If* it so happens that the PS3010 blows a power transistor, it will go to maximum current and may do damage to your multimeter,
blow it's fuse, etc. Quickly switch the powersupply off, and unplug. Let everything sit for 10 minutes or so to drain the voltage off C3.
If you have a diode-setting on your multimeter, use that position otherwise put it in the ohms setting. Put one probe on
the base (base of Q2 to Q5 are all connected together) and the other probe on the emitter of any of the 2N3772's. If any of
the four are shorted it shows for all of them. To check which transistor it is, disconnect the four wires going to R6 to R9. Put your
multimeter on the 'Diode' setting if possible and check each transistor between the 'base' and 'emitter'. You will find hopefully only one
shorted transistor. Replace it, and re-do the current adjustment. To prevent repetition of the same, adjust the PS3010 at 5A is good enough.
I'm looking into protecting each of the transistors and maybe a warning indicator of sorts.
Inside the enclosure I keep a little plastic container which contains some spare parts just in case I need it in the future.
The parts I use are the 723 IC, the zener diodes, 2N6388, and one 2N3772 power transistor. A medicine container will work real well. Why?
Well, just because everything is so-called short-circuit-protected it does not mean it can't happen, for example by a power surge, abuse when
in the 10A setting, or lightning. Murphy's applies here too. But on a positive note, this power supply is almost indestructible when used
within its boundaries.
Now, what can you do with this power supply? Anything you want. Charge regular NiCad or Lead-Acid batteries, power your projects, check the
current draw of a particular project, run all kinds of motors, styro-foam cutters, etc. It is limited only by your imagination.
Parts List:
Resistors:
1/4 Watt, Carbon, 5% (or better), unless otherwise indicated
R1 = 470 ohm, 1/2 watt
R2 = 2 K, trimmer pot
R3 = 5 K, potmeter (lin)
R4 = 560 ohm
R5 = 47 ohm
R6,R7,R8,R9 = 0.1 ohm, ww, 5%, 1-watt
R10,R11 = 0.33 ohm, ww, 5%, 10-watt
R12 = 470 ohm, potmeter (lin)
R13,R22 = 820 ohm
R14,R23 = 500 ohm, trimmer pot
R15 = 150 ohm
R16 = 100 ohm, trim pot
R17,R18,R19,R20 = see text
R21 = 5K, metalfilm, 1% (2 10K parallel 1%)
R24,R25,R26,R27 = See Text (non-variable: 25K trim pot)
R28,R29,R30,R31 = 3.3K
Capacitors:
C1,C2 = 3.3 nF, ceramic C7 = 470pF, ceramic (see text)
C3 = *8,200 uF/50V+, electrolytic C8 = 10 uF/63V, electrolytic
C4 = 1000 uF/63V, electrolytic C9 = 1 uF, foil type, see text
C5,C6 = 4.7 uF/63V, electrolytic C10 = 22 nF, ceramic
Semiconductors:
D1 = 1N4004
D2 = 1N4148
D3 = 1N3209 (or NTE5942) power diode, 15A+ (see text)
D5-D8 = Leds, (see text)
ZD1 = 1N4754A, Zener, 1 watt, 39V
ZD2 = 1N4736A, Zener, 250mW, 6.2/6.8V
Q1 = 2N6388 (or NTE263)
Q2-Q5 = 2N3772 (or NTE181)
L1,L2 = Ferrite Bead (see text)
IC1 = 723 (not the cmos type!)
BR1 = Bridge Rectifier (see text)
Miscellaneous:
M1,M2 = Panelmeter, see text
T1 = Transformer, Hammond 165S30 (30VAC/10A)
F1 = Fuse, 3.15A, slow-blow (depending on your transformer!)
S1 = Toggle switch, ON-OFF, DPDT, sub-mini
S2(a-b) = Toggle switch, ON-ON, DPDT
S3(a-b) = Toggle switch, ON-ON, DPDT
S4 = For use with one panelmeter: ON-ON, DPDT
Fuseholder, very large coolrib for the 4 power transistors, and Q1/D3 (isolated),
wire, solder, 2 knobs, instrument case, power cord, nylon stand-off's, etc.
The meter scales are re-scaled with rub-on lettering.
Possible Component Substitutes:
D1 = 1N4004, 1N4005, 1N4007, BY127, NTE116, NTE125
D2 = 1N4148, BAX13, BAX16, NTE519
D3 = Possible types: MUR2510, MUR3010CT, NTE6246, NTE6247, etc.
ZD1 = 1N4754A, NTE5086A, ECG5086A
ZD2 = 1N4736A, NTE5071A
Q1 = BD267A, TIP140, MJ2501, NTE263, NTE270
Q2 = NTE181
IC1 = uA723, LM723, NE723, NTE923D
In regards to buying your parts: You get what you pay for! Buy
decent components; the cheap 'made in China' crap will give you headaches
somewhere down the road if your power supply fails because of it!
Last Minute changes and other important info:
- At the right you see the AC stuff I used. Came from a defective UPS unit. It contained the on/off switch, fuse-holder,
an AC filter, and receptacle. Works just beautiful. Click on the picture for an enlarged view. The salvaged cool
rib is a little smaller in width then the enclosure so was just a nice opportunity to get a more professional look.
Click on the picture for an enlarged view.
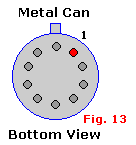
- If you decide to use the older 'metal-can' version of the 723,
the pin out is shown at the left. Just bent the legs in a 8-pin dip format, starting with pin 1 and it will
work fine.
- For the Led's I personally choose green for the low scales (0-6V/0-1A) and red for the high scales (1-30V/1-10A).
But hey, use whatever preference you have. High-brightness types is what I'm using, but again, use whatever you like.
- The bridge rectifier is one with a metal part attached for mounting on a coolrib. You can use 4 separate stud-mount
diodes of 75V/12-15A minimum. They
MUST be mounted
ISOLATED on a coolrib.
- Powerdiode D3: I used an older "stud-mount" type of 35Amps because I had it available and it has to go onto the
coolrib assembly. But use whatever you have laying around, just keep in mind it needs to be cooled and needs to be
a minimum of 20A. The 1N3899 goes up to 40A, but is overkill if you have to purchase it. The 1N3209 is no longer
available.
- Don't forget to mount R10/R11 away from the PCB. I used 1/4" (5mm) ceramic stand-offs. R10/R11 will get hot.
- Transformer T1: The voltage coming from the 30Vac transformer is 30x1.44pp = 43.2 V. The LM723's maximum voltage
is 37V. The circuitry connected to pin 12 of the 723 takes care of that and brings the voltage down to a safe level.
If you don't need 10 amps or 30V, feel free to change it to whatever you like. Don't know if you can obtain the
amperage with that low voltage. You may have to shop around. Otherwise get the 5A or 8A type. More than enough juice
for most of our applications.
- C3 (picture): Big sucker, but was needed for my application. Mine is a computer-grade 22000uF at 50V. Came
from a powersupply out of an old 'floor-model' tape-drive. But try anything decent you have or can obtain. A type
of about 8000 to 10000uF will do fine. If you're
thinking of combining two 4700uF or more capacitors, that's perfectly okay, just make sure that their values and
working voltages
*ARE* the same. (e.i. two 4700uF/63V caps in parallel will give 9400uF).
- Capacitor C7 is a so called 'compensation' capacitor and should not go beyond 1nF! Anything larger will result in
poor or no current limit circuitry or the inability to respond to transients which would feed massive currents into
the sense transistor (within the 723) whose E-B junction is directly across the (fractional-ohm in many cases) sense
resistor. The correct capacitor value for C7 is around 470pF (0.47nF) and can be ceramic or film.
- Panel meters: I decided to stick with the analog panel meters. I like to see exactly what i'm doing and in this
project they are just as accurate. The 'Volts' panelmeter will most likely be a 100-millivolt type with 30 or 60
scale stripes. The 'Amps' meter will probably be a 1-mA type with 50 or 100 stripes on the scale.
The internal resistance (Ri) of the meters is not at all important since anything with a build-in resistor or
resistance wire will be removed anyways.
- Coolrib. Here go the Transistors Q1 (2N6388), Q2 to Q5 (2N3772/NTE181), powerdiode D3, and the optional Fan(s).
The mounting holes for the fan and attaching it to
the enclosure is left to the builder. Make sure the
coolrib is mounted *isolated* from the enclosure. Nylon or ceramic standoff's are great!
- Cooling Fans: After some experimenting I decided to increase the 2 cpu fans with one more making the total 3.
I also decided to exchange the cpu fans, depicted in the photograph, for a different type which is a bit larger and
has more fins. My applications usually require 3 to 5 amps and so the whole cooling circuit with the fans now work
like a charm. I will likely modify the circuit and use a more common op-amp such as the 741, and create a printed
circuit board and parts layout for ease of use. Most types of thermistors will work so don't worry too much. You
just may have to play with the series resistance a bit. No big deal.
- Optional 3mm Led (any color) and 1K8 resistor for the Automatic Fan control (The "Autofan" circuit is the simplest
and works great using a 741!) Added this later after the front panel was already finished. Although you may be able
to hear the fans when they kick in, I prefer a visual indicator as well. Secondly, I like bells and whistles...(grin).
- And finally, just remember that this powersupply has lots of wires, most of them all coming from the coolrib.
It's very easy to make a wiring error, bad connection, wrong connection, etc. Just don't get frustrated. Sort out
one problem at a time. Remember to check with your multimeter that *ALL* semiconductors are *isolated* from the
coolrib. So when you have mounted your transistors and power diode, check to see that there is no-connection from its
case to the coolrib. Put one test probe on the coolrib and with the other test probe touch the case of all transistors
and D3 and check there is NO continuity. If you do have continuity somewhere check the mica washer and insulators.
On the four power transistors check that one insulator is at the bottom on one side and one at the top on the other
side (see pics). Don't forget the wiring for the fans and the thermistor if you decide to use the AutoFan temperature
controller. If all that checks out, Then, when you have checked the wired-up semiconductors on the coolrib, check it
again to make sure there is no wrong wiring connection shorting something out to the coolrib. Pay special attention
to D3. To insulate it, first put the mica washer on, then the heatshrink. Use thermal heatsink compound on all of
the semiconductors. When everything checks out take a brake and have a beer. You deserve it. After your brake
continue and feed the bundle of wiring into the case via the hole and grommet and proceed with wiring connections.
Use color-coded wire if you can and note all colors on your own schematic diagram. It really makes troubleshooting a
pleasure later on when needed.
Troubleshooting:
Okay, you're convinced you did everything right and the PS3010 is still not working. Frustrating, yes! On all the
problem emails most of it was sloppy or incorrect wiring, one case had the anode/cathode wiring to power diode D3
reversed. Several had a bad LM723 IC. I suggest to use a new 723. Saves on lots of headaches...
Below I have listed some common problems and suggestions for it. The new printed circuit board will have
'Test Points' on them to make troubleshooting easier (fall/winter 2008.)
Problem |
Check |
Notes |
On/Off switch S1 does nothing |
3.15A Fuse blown |
Replace with 3.5A, cord plugged in? |
One or more LED's are not lit |
LED's |
Connections are reversed |
6V position shows 0V |
C5, C6, D2, ZD1, IC1, R24 |
Replace if defective |
6V not variable, stays at max |
IC1, ZD2, R21, D2, C6, C7 |
Replace if necessary |
6V only variable after switching PS3010 OFF (no load) |
D3 |
Wires to anode/cathode reversed |
723 blows at power up |
T1, wiring |
Check wiring,caps,ZD1,D1,ZD2 |
723 blows at power up |
Wiring, C7, ZD2 |
Replace C7,R2,R22,R23,ZD2 |
No output voltage in 6V/30V |
Q1,Q2,Q3,Q4,Q5,D2,C6,IC1 |
Replace if defective |
30V position shows 0V |
C5, R26, D2, C7, ZD1, ZD2, IC1 |
Replace if defective. (for IC1 switch OFF first!) |
30V stays at max; not variable |
IC1, ZD1, ZD2, D2, C6, C7 |
If IC1: switch off, remove IC1, follow
adjustment procedure for 6V |
Current draw when varying R3 (no load) |
Short to ground |
PCB making contact with enclosure.
Make sure PCB is isolated |
Maximum current (no load) |
Short, incorrect wiring Q1 |
Unplug. C9, Check wiring. If leads on Q1
were reversed, replace |
Maximum current (no load) in all positions |
Short. Check wiring, Q1-Q5 |
Replace 723 on all shorts |
Case Histories:
Case #1. -- A client had the following problem: The PS3010 showed maximum voltage in the 6V and 30V ranges via the panel-meter. The panel meter
for current showed nothing, so I assumed it was not shorted. As it turned out, it drew maximum current. In my client's case 12A which blew the
main fuse in my Fluke multimeter twice before I noticed at a cost of $30 a piece! My first suspect were the power transistors (Q2-Q5) and the
Darlington (Q1). Couldn't find the problem. Took the whole coolrib apart and rebuild it from the ground up with new transistors. Checked the
power diode D3 which showed good. IC1 was defective and replaced it. I put the power back on and? No-go! Bloody h*ll! What gives?
Frustrated I started troubleshooting the wiring and then stopped. No need for it. This powersupply was working before it ended up on my bench.
I knew it must be a short somewhere else. I had another look at all other components and finally found the problem. The foil capacitor C9 was
shorted. Upon closer examination it was an older type with a working voltage of 50V. Not enough for spikes or when powered in the 10A position.
I replaced it with a polyester type and a 250V working voltage. Problem fixed!
Case #2. -- PS3010 came in the shop with only the 6V working but the needle on the panel meter slamming all the way to maximum. Potentiometer
R3 on the front panel could not vary the voltage. Also seems to draw way too much current. In the 6V position the maximum current should not
exceed 1 Amp. Before troubleshooting the 30V voltage position I had to fix the over-current first. I started trouble-shooting ZD1/ZD2,R4,R5, and
the darlington Q1 (2N6388). All turned out to be good. I continued with the power transistors. Found a short. Disconnected the four wires connected
from Q2,Q3,Q4,Q5 to the 0.1 ohm wire-wound resistors. Multimeter showed a short between base/emitter on Q4. Replaced the 2N3772 with a NTE181.
That problem fixed. Now the not-working 30V voltage position. Since the 723 IC cost 0.50 cent or less, I just replaced it with a new LM723. No
change. Checked the diode and zener diodes. ZD2, a 1N4736A 6.8V type, was shorted. Replaced it with a 1N4735A (6.2V) type. Problem fixed!
Case #3. -- Powersupply came in with no voltage or current in all settings. Client information indicated this powersupply used for high-amp
application, between 5A and max (10A). Upon examination it appeared the track on the circuit board going to pin 4 of the LM723 IC was burned and
blown away. D2, ZD2, and C7 were all defective. Replaced them. I removed the 723 also and replaced it with a new one. The LM723 IC wouldn't be
trustworthy after these critical components were defect. Repaired the foil-track on pin 4. I inserted a 50 ohm wire-wound 10 watt resistor on the
output jacks and put my multimeter in the 10A current setting. Carefully powered up the unit. Voltages seem to work with lots of current and
behaving erratic. Turned the power off and re-examined the printed circuit board on the bottom side (foil-side). After some head-scratching found
the problem. Customer build the powersupply very well and neatly but forgot to make sure the PCB was isolated from the case. After
adding some large, non-metal washers on the stand-offs and verifying the pcb was isolated from the case, the powersupply worked perfectly after
power-up.
And one final thing. Looking at the front panel above, you see three output jacks: Red (+), Black (-), and Green (chassis
ground). The green jack can be omitted if you don't need a chassis ground, OR if you have a transformer without a 'CT' (Center Tap)
connection. The 'CT' wire color on the transformer is either green or green/yellow and is located on the AC side (between the two black wires) and is
connected to the enclosure and the green jack on the front panel. Just don't confuse the black jack with the green jack. Chassis ground
is normally used to make a ground connection between different equipment, oscilloscope, or battery operated circuits. Your normal output jacks
are the RED and the BLACK.
Copyright © Tony van Roon, VA3AVR